Beim steirischen Lohnfertiger Heldeco sind es vor allem auch die Mitarbeiter gewesen, die in den letzten Jahren ein Maximum an Transparenz bei sämtlichen Abläufen im Unternehmen einforderten. Ein Anliegen, dem der Firmenchef Ing. Helmut Dettenweitz mit der Installation eines softwaretechnischen Überbaus über alle bereits bestehenden Systeme nachkam. Ein Optimierungsschritt, der sich mittlerweile in vielerlei Hinsicht positiv bemerkbar macht, wie er im nachfolgenden Interview verrät. Das Gespräch führte Sandra Winter, x-technik
Herr Dettenweitz, wie kam es zur Einführung des Lean Production Manager Systems (LPM) bei Heldeco?
Wir sind ein sehr innovatives und modernes Unternehmen mit extrem engagierten Mitarbeitern, die immer wieder interessante Verbesserungsvorschläge einbringen. Eine dieser Ideen war es, gewisse Informationen zentral zur Verfügung zu stellen, um die Abläufe in der Firma noch effizienter zu gestalten. Und da die Anforderungen unserer Kunden, u. a. bei Abnahmen und Prüfzertifikaten permanent steigen, erschien es in der Tat allmählich notwendig, dass jede Stabsstelle bzw. Mitarbeiter möglichst rasch sowie ohne Umwege zu den nötigen Informationen kommt.
Wie ließ sich diese Vision einer zentralen Datendrehscheibe dann tatsächlich realisieren?
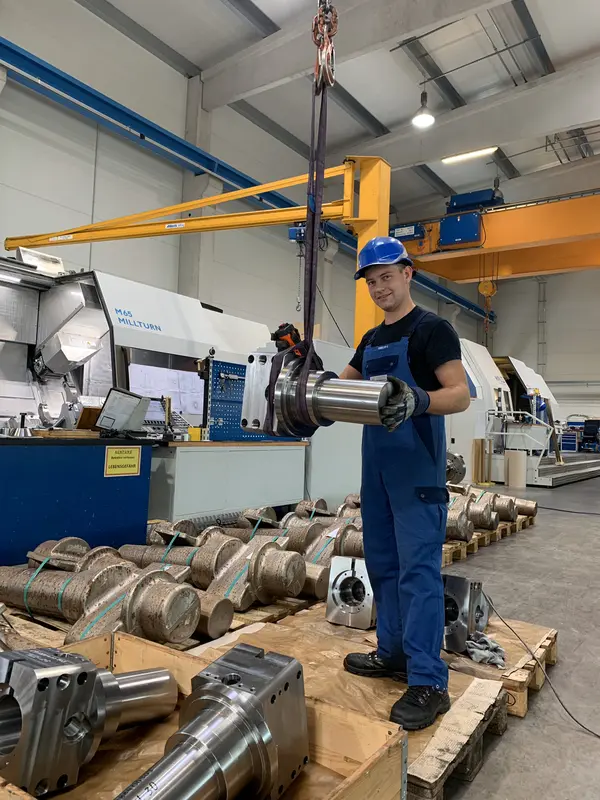
Als erstes überlegten wir uns, was wir optimieren wollen. Großes Potenzial orteten wir beispielsweise bei den Fertigungsunterlagen – angefangen von den Arbeitsplänen bis hin zu Kundenspezifikationen, Rüstplänen und Werkzeuglisten. Da wir vorwiegend im Projektgeschäft tätig sind, ist es natürlich eine ziemliche Herausforderung, all diese Papiere immer am aktuellen Stand zu halten. Teilweise erhalten wir ja sogar während der Bearbeitung noch Revisionsänderungen von Kunden. Solche Dinge waren in der Vergangenheit mit sehr viel Aufwand verbunden – Zeichnung austauschen, Laufkartenrevision ändern etc. – und das wollten wir so nicht mehr. Wir eruierten demzufolge, wie wir unsere gesamte Wertschöpfungskette, von der Angebotslegung bis zur technischen Überprüfung und Auslieferung, digital abbilden könnten. Dabei erwies sich die Firma Zebicom als perfekter Berater und Umsetzungspartner.
In Summe haben wir in den vergangenen Monaten rund zwei Millionen Euro in die Digitalisierung und in neue Fertigungstechnologien investiert. Mittlerweile werden den Mitarbeitern alle zu einem Projekt gehörenden Daten wie etwa Arbeitspläne, CNC-Programme, Fertigungsunterlagen und offene Aufgaben sowie die aktuelle Auftragsplanung und Maschinenbelegung in Echtzeit zur Verfügung gestellt.
Funktioniert Heldeco jetzt ganz papierlos?
Fast. Die Fertigungszeichnungen sind das Einzige, was wir teilweise noch auf Papier haben und das hat folgenden Grund: Wir sind auf die Bearbeitung komplexer Bauteile mit bis zu 20 Metern Länge und bis zu 30 Tonnen Gewicht spezialisiert. Dementsprechend groß sind oftmals die Zeichnungen, die als Vorlage dienen. Eine grafische Darstellung in A0-Format ist bei uns keine Seltenheit und solche Dimensionen lassen sich schwer auf einen Bildschirm übertragen. Da wäre vieles nicht mehr gut zu lesen.
Als Sie mit dem Lean Production Manager an den Start gingen, gab es da bereits bestehende Software-Systeme?
Ja, und das war auch eine der größten Herausforderungen, all diese Insellösungen unter ein einheitliches Software-Dach zu bringen. Ganz konkret galt es das ERP-System, die CAD/CAM-Lösungen, die Werkzeugverwaltung und -voreinstellung, die Messmittelverwaltung sowie die vorhandenen Siemens- und Heidenhain-Maschinen zu verheiraten und eine zentrale Datendrehscheibe zu generieren.
Wir haben oftmals Aufträge, für die wir 120 Werkzeuge und mehr benötigen. In solchen Fällen ist es jetzt natürlich von enormem Vorteil, wenn Werkzeuginformationen und Rüstvorgaben direkt und vollautomatisch zur jeweiligen Maschine weitergeleitet werden.
Etwaige Schnittstellenproblematiken konnten also erfolgreich gemeistert werden?
Einfach war es nicht, so viele unterschiedliche Lösungen auf einen gemeinsamen Nenner zu bringen, aber da die Firma Zebicom über sehr viel Erfahrung auf diesem Gebiet verfügt, gelang es uns letztendlich doch. Das ist eben die Schwierigkeit bei gewachsenen Systemen, wie wir sie haben. Könnte man bei Null starten, würde man manche Dinge vielleicht ein bisschen anders lösen.
Sind nun alle Punkte des LPM-Projekts abgehakt?
Nein, wir sind noch nicht ganz fertig, denn so ein System lebt ja. Kaum hat man eine Tür durchschritten tun sich dahinter weitere Möglichkeiten und Gestaltungsräume auf und so setzt sich das Ganze immer weiter fort. Es gibt immer wieder Verbesserungspotenzial. Anfangs erkennt man meist gar nicht, wie viel Potenzial in solchen Systemen tatsächlich schlummert, das zeigt sich oftmals erst im Laufe der Zeit.
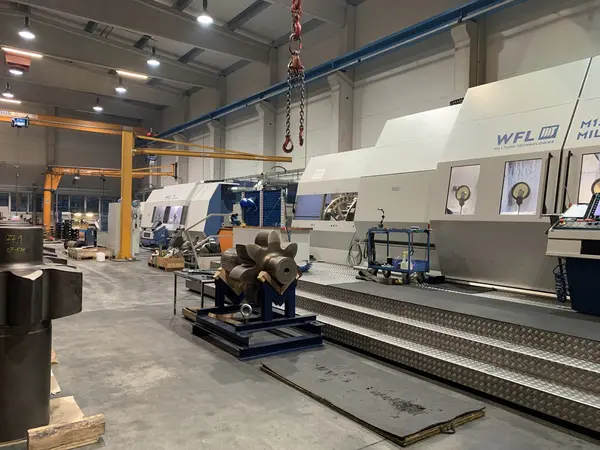
Momentan sind wir gerade dabei, die CNC-Programmverwaltung auf neue Beine zu stellen, um in Zukunft genau nachvollziehen zu können, welche Änderungen direkt an der Maschine vorgenommen wurden. In der Vergangenheit passierte es bei rund 15 % unserer Aufträge, dass in letzter Minute umprogrammiert wurde und bei solchen Aktionen fehlten letztendlich die Werkzeuglisten, weil für diese die Arbeitsvorbereitung verantwortlich zeichnete. Diese Informationslücke soll nun geschlossen werden. Insgesamt befinden sich derzeit ca. 15 offene Punkte auf unserer To-do-Liste. U. a. wollen wir bei diversen Kontrollen – Stichwort Maßprotokolle beispielsweise – und beim Thema auswärtige Fertigung nachschärfen.
Was hat sich seit der Einführung der zentralen Datendrehscheibe am meisten verbessert?
Die interne Kommunikation. Früher hatten wir oftmals mit mangelhaften Informationsweitergaben zu kämpfen, weil beispielsweise Zettel, auf denen ungeplante Vorfälle während einer Schicht notiert waren, aus unerfindlichen Gründen verschwanden. Heute hat bei uns jede Arbeitsstelle und nahezu jeder Mitarbeiter ein iPad. Damit kann sogar mit Foto dokumentiert werden, was passiert ist. Dabei erkennt das im Hintergrund laufende LPM-System sofort, bei welchem Fertigungsauftrag, Arbeitsvorgang und Artikel etwas schiefgelaufen ist. Für die Beschreibung des aufgetretenen Problems stehen vorgefertigte Textbausteine zur Verfügung. Die Weiterleitung der angegebenen Informationen an die zuständigen Vorgesetzten erfolgt automatisch per E-Mail.

Wir können mit dem Lean Production Manager aber auch unterschiedlichste Auswertungen machen. Wir wissen von jedem Mitarbeiter, bei welchem Auftrag er eingebucht ist und womit er sich aktuell beschäftigt: Rüstet er, muss er auf die Arbeitsvorbereitung oder auf weitere Kundenspezifikationen warten, wurde er bei seinem Tun unterbrochen, weil die Maschine aus irgendeinem Grund steht etc. Da gibt es sehr viele „Eventualitäten“, die der Mitarbeiter anstempeln kann und die uns letzten Endes beim Optimieren helfen. Würde sich beispielsweise herausstellen, dass unsere Mitarbeiter, die ja oftmals sehr große und schwere Teile zu handeln haben, aufgerechnet auf ein Jahr sehr viele Stunden damit zubringen, auf den Kran zu warten, wäre unter Umständen die Anschaffung eines zweiten Krans zu überlegen. Das Zebicom-System hilft uns also dabei, zu erkennen, an welchen Schrauben wir drehen müssen, um noch effizienter zu werden.
Inwiefern profitieren Heldeco-Kunden von der neu geschaffenen Transparenz?
Unsere Kunden profitieren davon, dass wir die Teile jetzt um einiges schneller durchschleusen können, weil die dafür nötigen Informationen nun viel zielgerichteter und größtenteils in Echtzeit fließen. Wir können auch prompt und kurzfristig auf Änderungen reagieren. Dabei hilft uns ein elektronischer Leitstand. Bei uns wird jeder Auftrag in eine digitale Plantafel eingelastet. Das bedeutet: Wir sehen ganz genau, was wann in unserem Betrieb passieren muss – wann wird programmiert, gefräst, die Qualität geprüft usw. Demzufolge kennt auch jeder Mitarbeiter seinen Arbeitsvorrat. Er weiß, für welche Tätigkeiten seine Zeitressourcen vorgesehen sind und kann sich somit perfekt auf das auf ihn Zukommende vorbereiten.
Was sind Ihrer Erfahrung nach mögliche Stolpersteine beim Thema Digitalisierung?
Zu viele Beteiligte und Meinungen, denn man verzettelt sich sehr schnell, wenn jeder nur sein Fachgebiet bzw. seinen Arbeitsplatz sieht. Wir gingen am Anfang ebenfalls zu blauäugig an die ganze Sache heran und dachten jeder müsse alles sehen. Die Mitarbeiter waren dann teilweise mit dieser Informationsflut sogar überfordert, die plötzlich auf sie zukam. Meine Empfehlung lautet demnach: Man sollte bei sämtlichen Digitalisierungsaktivitäten stets versuchen, sich den Blick aufs Ganze zu bewahren. Viele Ziele lassen sich vielleicht mit bereits bestehenden Systemen gut bzw. teilweise vielleicht sogar besser erreichen. Das gilt es ebenfalls zu checken, bevor man alles umkrempelt.
Inwieweit hat sich die gesamte Fertigungsbranche durch die Digitalisierung verändert?
Ich denke, dass die Digitalisierung für die meisten von uns Fluch und Segen zugleich ist. Mehr Transparenz führt zwar dazu, dass man schneller und zielgerichteter reagieren kann. Allerdings darf nun alles noch weniger Zeit und Ressourcen kosten. Der Stress ist also durch die Digitalisierung nicht weniger geworden.
Link zum Interview: hier